- JLR has worked with industry partners Dow and Adient to produce new seat foam for its luxury vehicles with closed‑loop recycled content, a first in the automotive industry (1)
- Polyurethane foams used in car seats are challenging when it comes to recycling as they are designed for durability
- Breakthrough is a result of JLR’s Circularity Lab, which aims to scale the repeated reuse and recycling of materials from its luxury vehicles to reduce emissions, eliminate waste and increase security of supply
- The JLR Circularity Lab, based at its HQ in Gaydon, brings cross‑functional teams together with expert partners and suppliers to innovate and overcome barriers for recoverability, reusability, repairability and recyclability collaboratively
- Production scale testing on the breakthrough closed‑loop seat foam is set to start in early 2025
- Circularity is a critical part of JLR’s approach to addressing environmental impacts beyond tailpipe emissions as it transitions to an all‑electric business, through its Reimagine strategy
Gaydon, UK – 27 November 2024: JLR has made a significant technical breakthrough in the closed‑loop recycling of polyurethane seat foam from its used vehicles by successfully reintegrating it back into the production of new seats.
In collaboration with Dow’s MobilityScience™ material innovations and global leader in automotive seating Adient, this is the first time closed‑loop seat foam content has been successfully used in automotive production.
Luxury vehicle manufacturer JLR is now putting the material through its full production process aiming to test its use at scale in pre‑production vehicles early next year.
Polyurethane foams are known to be challenging when it comes to recycling and are designed for durability, meaning they end up in landfill and can remain in the environment for several generations. By creating a closed‑loop supply chain, JLR will be able to reduce emissions, eliminate waste and enable a secure supply of low carbon seat foam for its vehicles.
The recycled foam will be one element to a new ‘circular seat’ that it is estimated will half CO2e emissions impact while maintaining high performance, avoiding over 44kg of CO2e per seat, the equivalent of charging almost three thousand smartphones2.
I am so excited about the potential of this way of working. It represents a collective commitment to doing things differently, challenging us to rethink our approach from all angles to find the solutions needed to design and build the cars of the future.
Close collaboration with experts from the recycling and materials science industries, with our supply chain partners, and colleagues from design and engineering is key – we need to work as a collective value chain to unlock meaningful change at scale. The knowledge and applications found demonstrate that full circularity is feasible and as a business this is critical to our transition.
Andrea Debbane
Chief Sustainability Officer, JLR
This collaboration highlights Dow's MobilityScience™ initiative to drive sustainable mobility through advanced material science. By leveraging our expertise and collaborating with Adient and JLR, we are developing technologies that support our net‑zero carbon emissions and our circular and renewable solutions goals. Through Dow's RENUVA™ sustainability program, Dow addresses the growing demand for recycled materials by converting End of Life waste into new raw circular materials, helping our customers meet their recycled content targets. Through chemical and advanced recycling processes, this breakthrough depolymerization closed‑loop recycling solution meets the requirements and maintains the superior comfort and quality of JLR seats.
Jon Penrice
Mobility President, Dow
At Adient, we are proud to lead the change in integrating closed‑loop recycled materials into our seating solutions. Our collaboration with JLR and Dow not only showcases our commitment to sustainability but also demonstrates how innovative partnerships can drive significant advancements in the automotive industry. By leveraging recycled polyurethane, we are setting new benchmarks for environmental responsibility while ensuring our products deliver the luxury and comfort our customers expect.
Mick Flanagan
Vice President Customer Group, Adient
The breakthrough is a result of ongoing research and testing at JLR’s Circularity Lab in Gaydon, which aims to reduce waste and boost the recyclability of its luxury vehicles.
Historically, vehicles have been designed with limited consideration for how easy it is to take them apart and separate materials once they reach end‑of‑life. The use of mixed materials that are difficult to separate, fixing methods and adhesives can make the challenge of reducing waste and recycling for reuse almost impossible.
JLR’s Circularity Lab aims to troubleshoot these challenges by bringing together cross‑disciplinary squads comprising sustainability, engineering, procurement and design. The teams disassemble vehicles in a collaborative ‘learn through doing’ approach, working closely with suppliers and experts in materials to understand and overcome the barriers to reuse and recycling.
Data is fed from the Lab directly into early decision‑making for vehicle development and testing for the technical feasibility of returning materials such as glass, steel, aluminium, and polymers back into its supply chain for reuse in the production of new vehicles whilst retaining the same high‑quality standards.
For example, initial tests on front bumpers found the same quality and performance could be achieved using a reduced number of polymers, saving 177,500 kg CO2e over a single model line3, whilst also saving £560,000 in cost. The approach means JLR will be able to deliver lower carbon bumpers physically on new cars from next year.
JLR has already had success in closed‑loop innovation through an award‑winning landmark project, which saw post‑industrial waste from aluminium body panel stamping recycled back to the supplier to be incorporated into new body panels. This involved technical innovations, such as the creation of a new aluminium grade that would be best suited to the closed‑loop process and could only have been achieved through true supply chain collaboration.
The Circularity Lab supports JLR’s Reimagine strategy which aims to set new benchmarks in environmental, societal and community impact for business. Central to this is its ambitious vision for circular economy, which aims to achieve a more resource efficient economy through the elimination of waste and repeated circulation of products and materials.
JLR has been an Ellen MacArthur Foundation Network Partner since 2023 and is applying circular economy principles to all aspects of its business, including its industrial transformation, which has seen thousands of pieces of equipment refurbished and redeployed to balance capability requirements, energy efficiency and CO2e impact as it prepares for its all‑electric future.
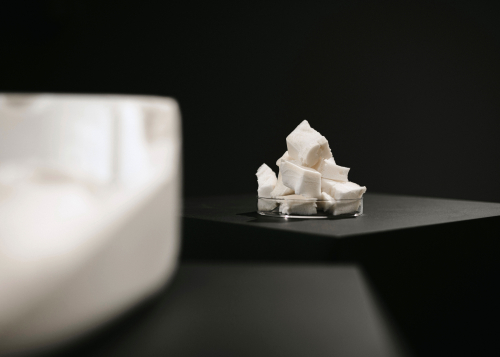
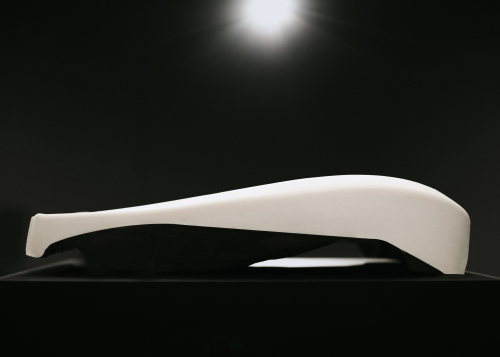
1 to the awareness of all parties involved this is the first time a PU molded foam for seating applications has been produced under these conditions. Initial lab testing proved technical feasibility based on 20% closed‑loop re‑polyol content. Next stage testing aims to increase percentage as high as viably possible.
2 Calculated using the USEPA Greenhouse Gas Equivalencies Calculator
3 Based on model line volume of 250,000 units