- Jaguar Land Rover partners with BASF in a pilot research project which aims to tackle the challenges of plastic waste
- ChemCycling project takes plastic waste and recycles it into premium material for potential use in future Jaguar and Land Rover models
- Recycled plastic material is tested on prototype production parts in the all‑electric Jaguar I‑PACE to ensure it meets Jaguar Land Rover’s exacting quality and safety standards
- Collaboration is a step towards delivering Jaguar Land Rover’s vision for a Destination Zero future
Whitley, UK, 19 July 2019: Jaguar Land Rover is trialling an innovative recycling process which converts plastic waste into a new premium grade material that could feature on future vehicles.
It’s estimated that the amount of waste plastic is predicted to exceed 12 million tonnes globally by 2050*. Today, not all of this plastic can be recycled for use in automotive applications – especially in vehicle parts that are required to meet the most exacting safety and quality standards.
Working in conjunction with chemical company, BASF, Jaguar Land Rover is part of a pilot project called ChemCycling that upcycles domestic waste plastic, otherwise destined for landfill or incinerators, into a new high‑quality material.
The waste plastic is transformed to pyrolysis oil using a thermochemical process. This secondary raw material is then fed into BASF’s production chain as a replacement for fossil resources; ultimately producing a new premium grade that replicates the high quality and performance of ‘virgin’ plastics. Importantly, it can be tempered and coloured making it the ideal sustainable solution for designing the next‑generation dashboards and exterior‑surfaces in Jaguar and Land Rover models.
Jaguar Land Rover and BASF are currently testing the pilot phase material in a Jaguar I‑PACE prototype front‑end carrier overmoulding to verify it meets the same stringent safety requirements of the existing original part.
Pending the outcome of the trials and progression in taking chemical recycling to market readiness, adoption of the new premium material would mean Jaguar Land Rover could use domestically derived recycled plastic content throughout its cars without any compromise to quality or safety performance**.
Plastics are vital to car manufacturing and have proven benefits during their use phase, however, plastic waste remains a major global challenge. Solving this issue requires innovation and joined‑up thinking between regulators, manufacturers and suppliers.
Chris Brown Senior Sustainability Manager
At Jaguar Land Rover, we are proactively increasing recycled content in our products, removing single‑use plastics across our operations and reducing excess waste across the product lifecycle. The collaboration with BASF is just one way in which we are advancing our commitment to operating in a circular economy.”
This is the latest example of Jaguar Land Rover’s commitment to addressing the challenge of waste plastic. The company has collaborated with Kvadrat to offer customers alternative seat options that are both luxurious and sustainable. The high‑quality material, available initially on the Range Rover Velar and Range Rover Evoque, combines a durable wool blend with a technical suedecloth that is made from 53 recycled plastic bottles per vehicle.
Jaguar Land Rover has already met its 2020 target for Zero Waste to Landfill for UK operations. This includes the removal of 1.3 million m2 – equal to 187 football pitches – of plastic from its manufacturing lineside and replacing 14 million single use plastic items in business operations.
Together, these efforts are driving towards Jaguar Land Rover’s vision for Destination Zero; an ambition to make societies safer and healthier, and the environment cleaner. Delivered through relentless innovation to adapt its products and services to the rapidly‑changing world, the company’s focus is on achieving a future of zero emissions, zero accidents and zero congestion.
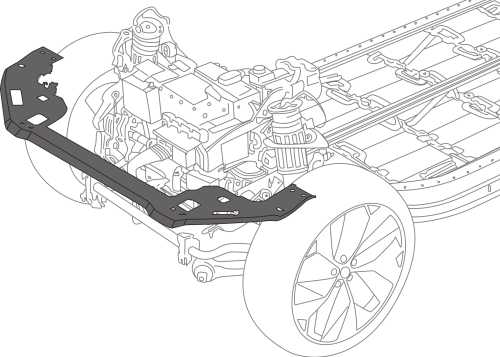
basf tw
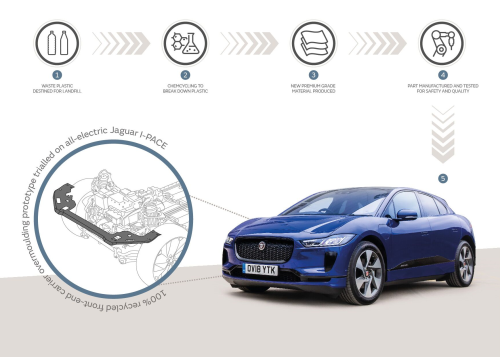